Table of Contents
Introduction
PROFIBUS (Process Field Bus) is a widely used fieldbus communication protocol in industrial automation systems. It’s essential for enabling real-time communication between controllers, sensors, actuators, and other devices in manufacturing, process control, and factory automation. If you’re preparing for an interview related to industrial automation, having knowledge of PROFIBUS protocol is crucial
In this post, we’ll cover the most common PROFIBUS protocol interview questions and answers that will help you ace your next interview.
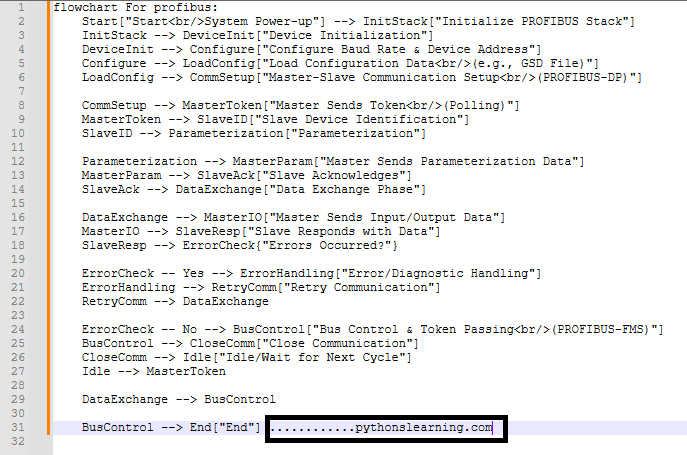
- What is PROFIBUS?
Answer:
PROFIBUS (Process Field Bus) is a standard for fieldbus communication in automation technology. It enables real-time communication between controllers (PLCs, DCSs) and devices such as sensors and actuators. It was developed in 1989 by Siemens and other automation companies. PROFIBUS is widely used in industrial automation, especially in factories, process plants, and machine building. - What are the different types of PROFIBUS?
Answer:
There are two main types of PROFIBUS: PROFIBUS DP (Decentralized Peripherals): Used for fast communication between control systems and distributed I/O devices.
PROFIBUS PA (Process Automation): Designed for communication in process industries, such as oil, gas, and chemicals. It supports intrinsic safety, making it suitable for hazardous environments. - How does PROFIBUS communication work?
Answer:
PROFIBUS uses a master-slave communication model. The master device (e.g., PLC) initiates communication by polling slave devices (e.g., sensors, actuators) for data. The slaves respond to the master’s requests, enabling a two-way exchange of information. PROFIBUS DP can support data rates of up to 12 Mbps, making it suitable for real-time control. - What are the key advantages of PROFIBUS?
Answer: High-speed data transfer (up to 12 Mbps for PROFIBUS DP).
Real-time communication, critical for time-sensitive industrial operations.
Supports both process and factory automation via PROFIBUS DP and PA.
Scalability: Can handle a large number of devices on a single network.
Robustness: Designed for harsh industrial environments. - Can PROFIBUS handle both digital and analog signals?
Answer:
Yes, PROFIBUS can handle both digital and analog signals. This flexibility allows it to be used in diverse automation applications, such as controlling motors (digital signals) and reading sensors (analog signals). - What is the difference between PROFIBUS DP and PROFIBUS PA?
Answer: PROFIBUS DP (Decentralized Peripherals) is optimized for fast, cyclic data communication between controllers and field devices in manufacturing systems.
PROFIBUS PA (Process Automation) is designed for process automation environments, supports intrinsically safe communication, and works with hazardous areas. - What is a PROFIBUS master and PROFIBUS slave?
Answer: PROFIBUS Master: This is typically the central controller (like a PLC or DCS) that manages network communication by polling slave devices.
PROFIBUS Slave: These are the field devices like sensors and actuators that respond to the master’s requests. - What type of physical layer does PROFIBUS use?
Answer:
PROFIBUS typically uses RS-485 as its physical layer for PROFIBUS DP, which supports twisted pair cables and up to 32 devices on a single segment. PROFIBUS PA uses a two-wire IEC 61158-2 physical layer that provides power and communication to devices, making it ideal for process industries. - How does PROFIBUS ensure data integrity and reliability?
Answer:
PROFIBUS uses cyclic redundancy checks (CRC) for error detection and has built-in mechanisms for handling communication retries, ensuring reliable data transmission. It also allows for redundancy in communication lines to prevent system failure due to cable faults. - What is the maximum number of devices that can be connected on a PROFIBUS network?
Answer:
A PROFIBUS DP network can support up to 126 devices (including masters and slaves), but the actual number depends on the baud rate, cable length, and the number of repeaters used. - What is the significance of GSD files in PROFIBUS?
Answer:
GSD (General Station Description) files contain the device-specific information that the master device needs to communicate with a PROFIBUS slave. These files are crucial for system configuration, as they provide details about the device’s capabilities, parameters, and communication settings. - What is PROFIsafe?
Answer:
PROFIsafe is a safety-oriented extension of PROFIBUS designed for use in safety-critical applications like emergency stop systems. It ensures that safety devices meet strict reliability and redundancy standards. - What are some common tools used for troubleshooting PROFIBUS networks?
Answer:
Common tools include: Bus analyzers: To monitor and diagnose communication issues.
Oscilloscopes: For checking signal integrity.
Diagnostic software: Provided by vendors to troubleshoot network performance and device status.
Network testers: To measure voltage, noise levels, and network quality. - How is PROFIBUS different from other industrial communication protocols?
Answer:
Compared to other protocols like Modbus or Ethernet/IP, PROFIBUS offers higher speeds, real-time capabilities, and supports both discrete and process automation. It also has redundancy features and better integration for hazardous environments with the PA variant.
Conclusion
Understanding PROFIBUS is crucial for anyone working in industrial automation. By preparing for these common interview questions, you’ll have a solid foundation to answer technical queries related to this widely-used protocol. Good luck with your interview preparation!
FAQs on PROFIBUS Protocol
- What is the difference between PROFIBUS and PROFINET?
PROFIBUS is a fieldbus protocol, while PROFINET is Ethernet-based and provides faster, larger-scale communication in industrial automation. - Can PROFIBUS be used in hazardous areas?
Yes, PROFIBUS PA is designed specifically for hazardous environments and supports intrinsic safety.